Friday, November 22, 2024
How to Build a Pallet Shed with Free Plans: Simple and Affordable
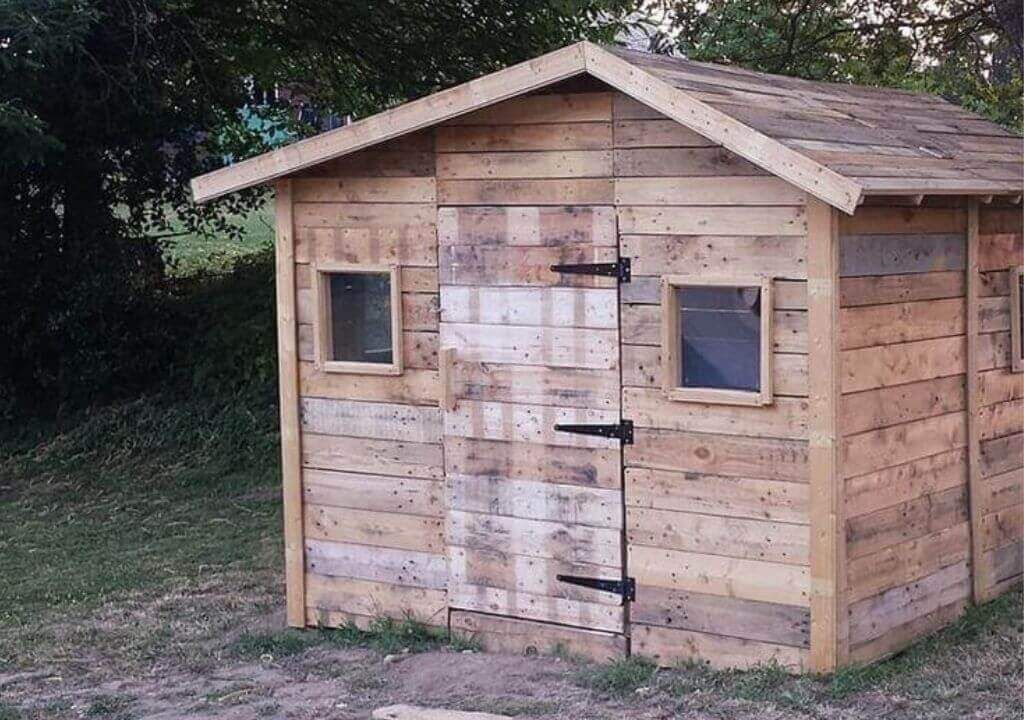
Constructing a Pallet Shed Utilizing Free Plans: A Guide to Economical Construction
The allure of a cost-effective and functional storage solution is undeniable. A pallet shed, constructed using reclaimed materials and readily available free plans, offers a compelling alternative to commercially-built structures. This comprehensive guide details the process of building a robust and aesthetically pleasing pallet shed, emphasizing practicality and minimizing expenses. While utilizing free plans necessitates a degree of DIY expertise, this guide aims to simplify the process for even moderately experienced builders.
I. Planning and Preparation: Laying the Foundation for Success
Before embarking on construction, meticulous planning is paramount. This stage encompasses several key aspects that directly influence the project's outcome and longevity.
A. Sourcing Materials: The Heart of Cost-Effectiveness
The cornerstone of a budget-friendly pallet shed lies in acquiring suitable pallets at minimal or no cost. Several avenues exist:
- Local Businesses: Contact nearby supermarkets, grocery stores, and distribution centers. Many are willing to relinquish used pallets rather than dispose of them.
- Construction Sites: Construction sites often have a surplus of pallets. Inquire politely about their disposal practices and potential availability.
- Online Classifieds: Websites and applications dedicated to classified advertisements often feature free or low-cost pallet listings.
- Recycling Centers: Some recycling centers may offer pallets for a small fee or even for free.
B. Selecting a Suitable Location: Considerations for Placement
The shed's location profoundly affects its functionality and longevity. Factors to consider include:
- Accessibility: Ensure easy access for loading and unloading items.
- Ground Conditions: Level, well-drained ground is essential for a stable foundation. Consider using gravel or concrete pavers for added stability, especially in softer soils.
- Sun Exposure and Weather Protection: Position the shed to minimize direct sunlight and exposure to prevailing winds and rain. Consider the orientation in relation to potential snow accumulation.
- Local Regulations: Check local building codes and zoning regulations concerning shed construction and placement.
C. Choosing the Right Free Plans: A Foundation for Success
Numerous free pallet shed plans are available online. Thoroughly review several options to select a design matching your needs and skillset. Consider the following criteria:
- Dimensions: Choose a size appropriate for your storage requirements and the available space.
- Complexity: Opt for a plan that aligns with your construction experience. Beginners should prioritize simpler designs.
- Material List: Ensure the plan provides a detailed list of materials needed, including lumber quantity and dimensions.
- Detailed Instructions: Select plans with clear, step-by-step instructions and accompanying diagrams.
II. Construction Process: Building Your Pallet Shed
The construction process follows a logical sequence, building upon the preparatory work. Careful attention to detail is critical for a structurally sound and aesthetically pleasing result.
A. Foundation Construction: Ensuring Stability
A solid foundation is essential for a durable shed. While a simple gravel base is sufficient for lighter sheds, consider a more robust concrete slab for heavier structures or unstable ground. Ensure the base is level and adequately sized for the shed's footprint. This stage may require specialized tools and materials depending on the chosen foundation type. Refer to your chosen plan for specific requirements.
B. Pallet Preparation and Assembly: The Core Structure
Before assembling the pallets, inspect each one again for damage. Repair any significant damage using screws, wood glue, and wood filler. The assembly process typically involves connecting pallets using additional lumber and appropriate fasteners (screws, nails, or bolts). Pay close attention to the free plan's specifications for creating a structurally sound frame. Using a level ensures squareness and prevents warping. Pre-drilling holes before fastening reduces the risk of splitting the wood.
C. Roofing and Siding: Weather Protection and Aesthetics
The roofing system is crucial for protecting the shed's contents from the elements. The chosen roofing material (tar paper, corrugated metal, or recycled materials) will influence the construction method. Properly securing the roofing material is vital for preventing leaks and damage. Siding can be added for extra protection and improved aesthetics; pallet wood itself can be used for siding if creatively arranged. Consider using weather-resistant paint or sealant to enhance longevity.
D. Door and Window Installation: Access and Ventilation
Install the door and windows according to the free plan's specifications. Ensure proper sealing around the frames to prevent drafts and water infiltration. Use appropriate hinges and hardware for a secure and functional opening and closing mechanism. Consider adding latches or locks for security. Appropriate ventilation is important to prevent moisture buildup and potential damage to stored items.
III. Finishing Touches and Maintenance: Enhancing Longevity
The final stages involve refining the shed and implementing preventative maintenance to extend its lifespan.
A. Finishing and Aesthetics: Enhancing Visual Appeal
Consider adding finishing touches such as paint, stain, or sealant to protect the wood and enhance the shed's aesthetics. Select weather-resistant coatings designed for outdoor use. A fresh coat of paint can significantly improve the overall appearance and protect the wood from the elements.
B. Regular Maintenance: Ensuring Durability
Regular maintenance is crucial for prolonging the shed's life. This includes inspecting for damage, repairing any cracks or loose boards, and reapplying sealant or paint as needed. Regular cleaning prevents the buildup of dirt and debris, reducing the risk of deterioration. Inspect the foundation for settling and address any issues promptly.
C. Considerations for Advanced Features
Depending on the chosen plan and your skill level, you can incorporate advanced features like shelving, a work bench, or even electricity. However, ensure your electrical work adheres to all local codes and regulations. Proper grounding and wiring are essential for safety. Consult with a qualified electrician if you lack experience in electrical work.
Building a pallet shed using free plans provides a rewarding and cost-effective approach to creating valuable storage space. By meticulously following the planning and construction steps detailed above, you can construct a durable and aesthetically pleasing structure that meets your needs for years to come. Remember that safety should always be a priority; wear appropriate protective gear and follow safe working practices throughout the entire construction process.
Thursday, November 21, 2024
DIY Lean-To Shed: Affordable and Functional Backyard Shed Plans
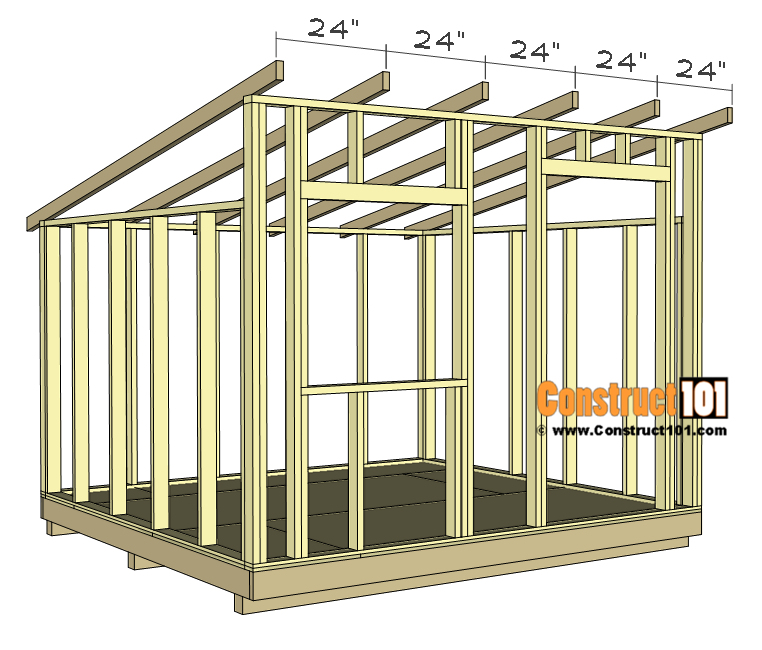
DIY Lean-To Shed: Affordable and Functional Backyard Shed Plans
Tired of clutter piling up in your garage or overflowing from your basement? Yearning for extra storage space without breaking the bank? A lean-to shed might be the perfect solution! This versatile structure, attached to an existing wall (like your house or garage), offers surprisingly generous storage space at a fraction of the cost of a freestanding shed. This guide provides comprehensive, easy-to-follow plans for building your own affordable and functional lean-to shed, transforming your backyard clutter into organized calm.
Planning Your Lean-To Shed
Before you even grab a hammer, careful planning is key. Determine the size and location of your future shed. Consider the available wall space, local building codes (check with your city or county), and the overall aesthetic of your property. A smaller lean-to might suffice for storing gardening tools and seasonal decorations, while a larger one can handle bicycles, outdoor furniture, or even a small workshop. Think about access â" will you need a door large enough to accommodate bulky items? Sketch a detailed plan, noting dimensions, materials, and placement of doors and windows. This initial step saves time and avoids costly mistakes down the line.
Essential Considerations:
- Size and Dimensions: Carefully measure your available wall space and plan accordingly.
- Building Codes: Check local regulations concerning shed construction, permits, and setbacks.
- Materials: Choose affordable yet durable materials like pressure-treated lumber for the frame and a weather-resistant roofing material.
- Access: Plan for easy access with appropriately sized doors and a convenient path.
Gathering Materials and Tools
Building a lean-to shed requires a mix of common building materials and tools. A detailed list will vary based on your specific design, but here's a general overview: Pressure-treated lumber forms the sturdy foundation. Opt for various sizes depending on the framework's needs. You'll also need roofing materials, like asphalt shingles or metal sheeting, ensuring weather resistance. Fasteners such as screws and nails are essential for securing everything together. For the floor, consider using plywood or concrete. Finally, gather your tools: a measuring tape, saw (circular saw or hand saw), drill, level, hammer, and safety glasses are crucial for a safe and efficient building process. Remember to always prioritize safety by wearing appropriate protective gear.
Construction Steps: Building Your Lean-To Shed
With your plans and materials ready, it's time to build! Start by constructing the frame, using your pressure-treated lumber. Begin by securing the base plates to the existing wall, ensuring a level foundation. Then, erect the supporting posts and attach the roof rafters. Creating a strong and level frame is paramount for stability. Once the frame is complete, attach your chosen roofing material, following manufacturer instructions. Lastly, install the siding (if desired), adding a layer of protection and enhancing the shedâs aesthetic appeal. Remember to meticulously check your work at each stage, ensuring everything is square and level.
Finishing Touches and Maintenance
Once your lean-to shed stands proudly in your backyard, add the finishing touches. A door, whether pre-hung or custom-built, provides security and access. Consider adding windows for ventilation and light. Apply a sealant or weatherproof paint to protect the wood from the elements, prolonging its lifespan. Regular maintenance is key: check for any loose screws or damaged parts and address them promptly. This proactive approach guarantees your lean-to shed will serve you faithfully for years to come, offering convenient and affordable extra storage.
DIY Pallet Shed: How to Build a Sturdy Shed with Pallets
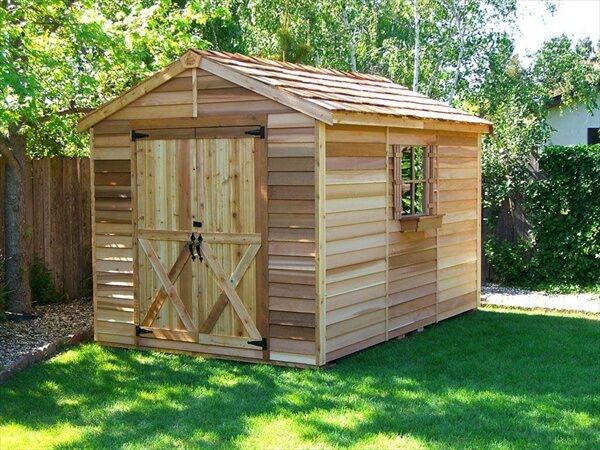
DIY Pallet Shed: How to Build a Sturdy Shed with Pallets
Hey there, fellow DIY enthusiasts! So you're thinking about building a shed, huh? And you're eyeing those free pallets stacked up everywhere? Great idea! Building a shed from pallets can be a fantastically budget-friendly project, and it's surprisingly rewarding. This guide will walk you through the process, from planning to the final touches. Let's get started!
1. Planning Your Pallet Shed: Dreams and Reality
Before you dive headfirst into hammering and sawing, let's talk about planning. This is the crucial step where you avoid costly mistakes down the line. Think of it as laying the foundation (pun intended!) for your amazing pallet shed.
1.1 Size and Location:
First things first: how big do you want your shed to be? Consider what you'll store inside. A small shed for gardening tools is different from a larger one for bikes and lawnmowers. Also, where will it be located? Check local building codes and ensure you have enough space, access to utilities (if needed), and consider sun exposure and drainage.
1.2 Pallet Selection:
Not all pallets are created equal! You'll need to gather a significant number, and the quality matters. Look for sturdy pallets made of strong, untreated wood. Avoid pallets marked with a "HT" stamp (heat treated) which can be harder to work with. Inspect each pallet carefully for rot, damage, or loose boards. Donât be afraid to be picky! The sturdier your starting material, the stronger your shed will be.
1.3 Design and Sketch:
Even a simple shed needs a plan. A quick sketch will help you visualize the structure and calculate the number of pallets you'll need. Think about the door placement, window placement (if any), and the overall layout. You can find tons of inspiration online â" search for "pallet shed plans" on Pinterest or Google Images. Don't be afraid to modify existing plans to fit your needs and available pallets.
2. Gathering Your Tools and Materials
With your plan in hand, it's time to gather the necessary tools and materials. Besides the pallets themselves, youâll need a few essentials:
- Measuring tape: Accurate measurements are key.
- Hammer: A good claw hammer is indispensable.
- Screws & Drill: Screws are much stronger than nails for this kind of project. A cordless drill makes things significantly easier.
- Circular saw or reciprocating saw: For cutting pallets to size, a circular saw is ideal, but a reciprocating saw will do the job.
- Safety Glasses and Gloves: Always prioritize safety!
- Level: To make sure your shed is... well, level.
- Post hole digger or shovel: If youâre creating a foundation.
- Wood sealant or paint (optional): To protect your shed from the elements and give it a nicer look.
- Concrete mix or gravel (optional): For a more permanent foundation.
Remember to check your local hardware store for any additional tools or materials that might be necessary based on your specific design.
3. Construction: Building Your Pallet Shed
Now for the fun part! Remember, safety first. Wear your safety glasses and gloves at all times. Let's break down the construction into manageable steps:
3.1 Foundation:
You have several options for your foundation. A simple gravel base is sufficient for a small shed, especially if it's not going to be heavily loaded. For added stability and protection from moisture, you could construct a small concrete slab. Consider your soil type and local climate when making this decision.
3.2 Frame Assembly:
Carefully dismantle some of your pallets to obtain usable boards. Start by building the frame of your shed, using these reclaimed boards and screws. Make sure the frame is square and level at each stage. This will provide the solid base for the pallet walls.
3.3 Wall Construction:
Attach the pallets to your frame. You may need to cut and adjust some pallets to fit perfectly. Ensure that you secure the pallets firmly using screws. Consider staggering the pallets slightly to add extra strength and a more visually appealing result.
3.4 Roof Construction:
Constructing the roof is similar to the walls. You can use whole pallets or cut boards, depending on your roof design. Make sure the roof has sufficient slope to allow for water drainage. Consider using a waterproof membrane or roofing felt for additional weather protection.
3.5 Door and Window Installation (if applicable):
If you're incorporating a door or windows, plan their placement carefully during the framing stage. You might need to cut openings in the pallets, ensuring the structural integrity of the shed isn't compromised. Hang the door securely and install window frames with weather-resistant sealant.
4. Finishing Touches
Once the basic structure is complete, it's time to add the finishing touches:
- Seal and Paint: Apply a wood sealant or paint to protect your shed from the elements and enhance its appearance. This will also help to prolong its lifespan.
- Flooring (Optional): Add a simple floor using plywood or reclaimed wood. This will keep your belongings dry and clean.
- Shelving (Optional): Add shelves to maximize storage space. You can construct these from more reclaimed pallet wood.
- Hardware: Install any necessary hardware such as hinges, handles, and locks.
Commonly Asked Questions
Q: How long does it take to build a pallet shed?
A: This varies greatly depending on the size and complexity of your shed, and your experience level. A small simple shed might take a weekend, while a larger, more complex project could take several weekends or even longer.
Q: Are pallet sheds durable?
A: With careful planning and construction, a pallet shed can be surprisingly durable. Using sturdy pallets and proper construction techniques ensures a strong and long-lasting structure. However, it will likely need more maintenance than a professionally built shed.
Q: Are there any permits required?
A: Building codes vary by location. Check with your local authorities to determine if permits are needed for your project. Size and location will often determine this.
Q: Can I use treated pallets?
A: While possible, using treated pallets can be problematic. Some treated lumber contains chemicals that could be harmful, especially if the shed will store food or items that come into contact with the skin. Unless you are absolutely certain of the type and safety of the treatment, it's best to avoid them.
Q: What about pest control?
A: Pallets can sometimes harbor insects or pests. Thoroughly inspect your pallets before use and consider treating them with a wood preservative before assembly to prevent any future issues.
There you have it! Building a pallet shed is a rewarding project that allows you to create something useful and unique. Remember to prioritize safety, plan carefully, and have fun with the process. Happy building!
How to Build a DIY Pallet Shed for Your Garden and Yard Equipment

Build Your Dream Pallet Shed: A DIY Guide for Garden Storage
Tired of tangled garden hoses and overflowing toolboxes cluttering your yard? Dreaming of a neat, organized space to store your outdoor equipment? Building a DIY pallet shed is a surprisingly achievable project that offers a stylish and practical solution. This guide will walk you through each step, transforming reclaimed pallets into a functional and attractive addition to your garden. Get ready to unleash your inner builder!
Planning Your Pallet Shed
Before you even touch a hammer, meticulous planning is crucial. Consider the size you need based on the equipment you plan to store. Sketch a design, noting the dimensions and the placement of doors and windows (if desired). Accurate measurements are paramount for a successful build. Next, gather your materials. Source sturdy, heat-treated pallets â" check for any signs of rot or damage. Youâll also need screws, a drill, a saw (circular saw recommended for speed and accuracy), measuring tape, a level, and possibly a post hole digger if you plan on a permanent installation. Consider adding extra features like a roof overhang for added weather protection.
Choosing the Right Pallets
Not all pallets are created equal. Prioritize pallets marked with the HT stamp, indicating heat treatment and ensuring they're safe for use. Avoid chemically treated pallets as they may release harmful substances. Inspect each pallet carefully for rot, damage, or loose boards before incorporating them into your structure. The sturdier the pallets, the more robust your shed will be.
Constructing the Frame
With your plan and materials assembled, itâs time to build the frame. Start by laying out the base using your chosen pallets, ensuring they're level and square. Secure them together using screws, driving them at an angle for increased strength. Once the base is secure, construct the walls, using additional pallets to create the desired height. Remember to maintain a consistent spacing between the pallets to ensure structural integrity. Use the level frequently to keep everything perfectly aligned.
Securing the Walls and Roof
Attach the walls to the base frame using long screws, reinforcing the corners with extra support. For the roof, you can use additional pallets or consider a more traditional roofing material like plywood or corrugated metal sheeting for added weather protection. If using pallets for the roof, consider overlapping them to ensure water runoff. Secure the roof structure firmly to the walls.
Adding Finishing Touches
Once the basic structure is complete, you can personalize your shed. Consider adding a door using reclaimed pallet wood or purchasing a pre-made door. Install hinges and a latch for security. You might also add windows for ventilation and light. Sand any rough edges to prevent splinters. A coat of weather-resistant sealant or paint will protect your shed from the elements and enhance its aesthetic appeal.
Personalization Ideas
Let your creativity shine! Consider these additions:
- Adding shelves for organized storage.
- Painting the shed a vibrant color to complement your garden.
- Installing a simple locking mechanism for added security.
- Adding a small window for extra light and ventilation.
Enjoy Your New Pallet Shed!
Congratulations! Youâve successfully built your own DIY pallet shed. Enjoy the satisfaction of a job well done and the added organization and charm it brings to your outdoor space. Remember to regularly inspect your shed for any signs of wear and tear, and perform necessary maintenance as needed to ensure its longevity.
Budget-Friendly 10x12 Pallet Shed Plans for Creative Builders

Budget-Friendly 10x12 Pallet Shed Plans for Creative Builders
Constructing a shed can be a significant investment, but resourceful builders can achieve substantial savings by utilizing readily available and inexpensive materials such as reclaimed pallets. This comprehensive guide details the design and construction of a budget-friendly 10x12 pallet shed, emphasizing creative solutions and cost-effective strategies for the discerning DIY enthusiast.
I. Planning and Design Considerations
Before embarking on the construction, meticulous planning is paramount. This stage encompasses site selection, design refinement, material acquisition, and tool preparation. Careful consideration at this preliminary stage ensures a smoother, more efficient, and ultimately more successful build.
A. Site Selection and Preparation
The chosen site must be level and adequately sized to accommodate the 10x12 ft footprint of the shed, plus sufficient space for construction and maneuverability. Consider factors such as proximity to power sources (if electrical components are planned), drainage, and sunlight exposure. Proper site preparation involves leveling the ground, removing vegetation, and potentially compacting the soil to provide a stable foundation. A well-prepared site significantly reduces construction challenges and ensures the shed's longevity.
B. Design Refinements and Customization
While this guide provides a foundational design, adjustments can be made based on individual needs and preferences. For instance, the inclusion of windows can enhance natural light and ventilation. Consider the desired level of insulation, which directly impacts cost and energy efficiency. The inclusion of a door, shelving, or workbenches will require careful planning to integrate these elements seamlessly into the overall design. Detailed sketches and diagrams are crucial for visualizing the final product and coordinating the construction process.
C. Material Acquisition and Cost Optimization
Pallet sourcing is a key aspect of cost reduction. Locate free or low-cost pallets from local businesses, construction sites, or online classifieds. Inspect each pallet carefully for structural integrity; damaged or rotted pallets should be avoided. Supplementing pallets with inexpensive lumber for framing, roofing, and trim can be necessary. Explore options for discounted or reclaimed lumber from salvage yards or lumber mills. Hardware procurement should be approached strategically; buying in bulk often results in cost savings. A detailed materials list is essential for accurate budgeting and efficient purchasing.
D. Essential Tools and Equipment
Before commencing, ensure you possess the necessary tools. These include, but are not limited to: a hammer, pry bar, saw (circular saw, hand saw, or reciprocating saw), measuring tape, level, drill, screws, nails, safety glasses, gloves, and work boots. Consider renting specialized tools, such as a post hole digger or concrete mixer, if the budget constraints do not allow for purchasing. A well-equipped workspace minimizes delays and enhances safety.
II. Foundation and Framing
A robust foundation and sturdy frame are fundamental to a structurally sound shed. The chosen foundation type should align with the ground conditions and the shed's anticipated load. The framing structure utilizes the reclaimed pallets, supplemented where necessary with additional lumber.
A. Foundation Construction
Several foundation options exist, ranging from simple gravel pads to more permanent concrete slabs. A gravel pad is the most budget-friendly solution, requiring minimal materials and labor. Level the ground and compact the soil before laying a layer of gravel, ensuring proper drainage. For increased stability, consider using concrete blocks as a base for the pallet structure. A concrete slab provides the most robust foundation but requires more time, effort, and material cost.
B. Pallet Preparation and Framing
Thoroughly inspect all pallets for structural integrity, removing any loose nails or splinters. Disassemble the pallets, separating usable planks and discarding damaged pieces. The frame can be constructed using a combination of pallet wood and new lumber. The use of pressure-treated lumber for the base frame is recommended to resist rot and insect damage. Assemble the frame using appropriate joinery techniques, ensuring squareness and stability at all stages. Accurate measurements and precise cuts are critical for a robust structure.
C. Wall Construction and Pallet Integration
Once the frame is complete, the pallet walls can be constructed. Pallet planks can be attached directly to the frame, creating a rustic aesthetic. Consider using additional framing lumber to strengthen the pallet wall structure and ensure proper alignment. Gaps between pallets can be filled with insulation or caulking to improve energy efficiency and weather resistance. Strategic placement of doors and windows should be incorporated during this phase.
III. Roofing and Finishing Touches
Roofing and finishing touches are the final stages that transform the structure into a functional and aesthetically pleasing shed. The roof design should be compatible with local weather conditions, ensuring adequate protection from rain, snow, and wind.
A. Roofing Options and Installation
Several roofing options exist, ranging from simple corrugated metal sheets to more complex shingle roofing systems. Corrugated metal is cost-effective and durable, ideal for this budget-conscious project. Ensure proper ventilation to prevent moisture buildup. The roof structure should be adequately supported to withstand anticipated loads. Securely attach the roofing material, ensuring watertight seals at all joints.
B. Finishing Touches and Customization
Once the roof is complete, add finishing touches to enhance the shed's functionality and appearance. This may involve painting or staining the exterior, adding trim for aesthetic appeal, installing a door and windows, and constructing interior shelving or workbenches. Consider adding weather stripping around doors and windows to further enhance weather resistance. The level of customization is largely dictated by budget and preferences.
IV. Safety Precautions
Safety should remain paramount throughout the construction process. Wear appropriate personal protective equipment (PPE), including safety glasses, gloves, and work boots. Use caution when handling power tools and sharp objects. Ensure proper ventilation in enclosed spaces. Seek assistance for tasks that are beyond your skill level. A safe work environment ensures project completion without injury or incident.
By following these detailed plans and employing resourceful techniques, creative builders can construct a functional and aesthetically pleasing 10x12 pallet shed at a significantly reduced cost. Remember that careful planning, diligent execution, and attention to detail are key to a successful project.
Basic Shed Plans for Beginners: A Guide to Easy Outdoor Projects
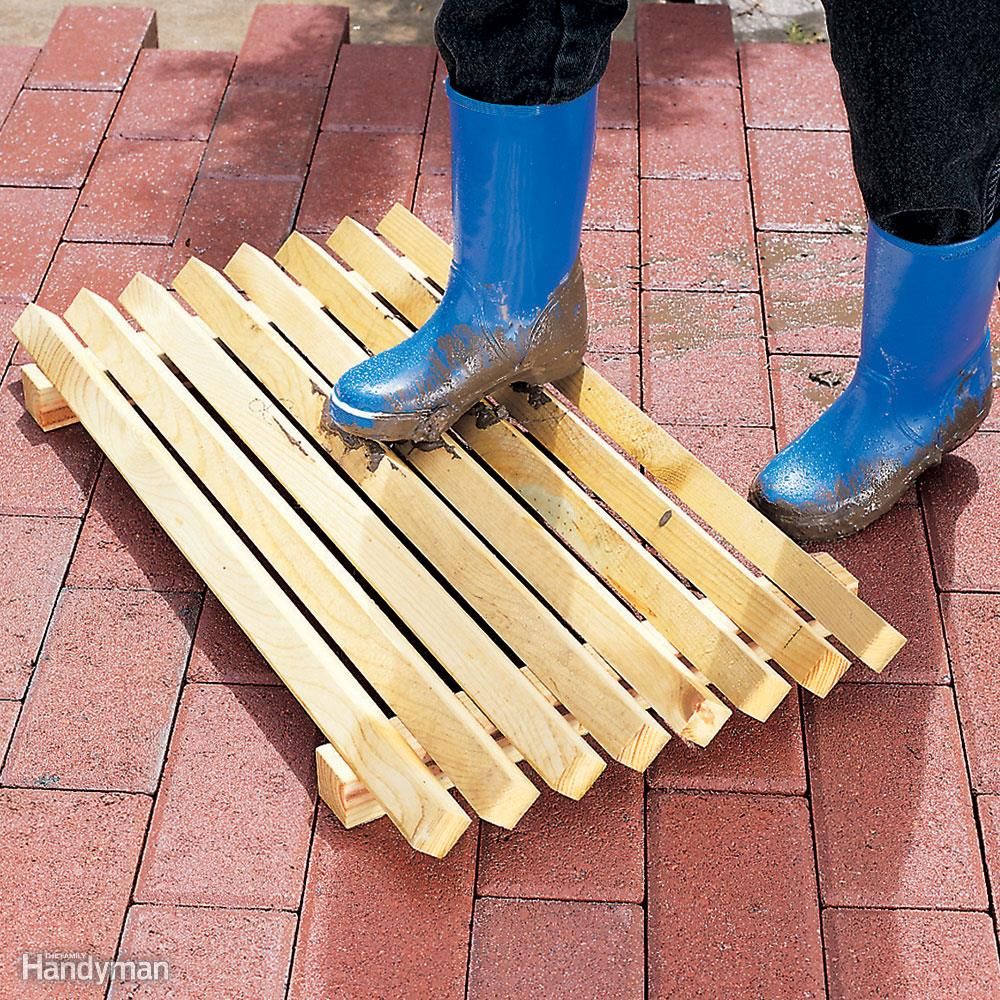
Basic Shed Plans for Beginners: A Guide to Easy Outdoor Projects
Building your own shed is a rewarding experience, offering a sense of accomplishment and a valuable addition to your property. This guide provides beginners with straightforward plans for constructing a simple yet functional shed. We'll walk you through the process step-by-step, demystifying the seemingly daunting task and empowering you to create your own outdoor storage solution.
Planning Your Shed Project
Before you even think about grabbing a hammer, careful planning is crucial. Start by determining the size and location of your shed. Consider your storage needs â" will you primarily store gardening tools, bicycles, or something else entirely? A larger shed provides more space but demands more materials and effort. Choosing the right location is equally important. Ensure the area is level, allows for adequate sunlight (if desired), and complies with any local building codes and regulations. Finally, sketch a basic design â" even a simple drawing will help you visualize the project and estimate the materials required. Don't underestimate the power of visualization; it helps prevent costly mistakes down the line.
Gathering Your Materials and Tools
Once you have your plans, create a detailed materials list. This list will include lumber (pressure-treated for longevity), screws, nails, concrete for the foundation, and any other desired features like a door and window. Consider pre-cutting lumber at your local lumberyard to save time and effort. Regarding tools, you'll need the basics: a measuring tape, level, saw (circular saw is ideal but a hand saw works in a pinch), drill, screwdriver, shovel, and possibly a post-hole digger if you're opting for a more permanent foundation. Always prioritize safety and use appropriate personal protective equipment (PPE) throughout the project. Thorough preparation minimizes frustration and keeps the project moving smoothly.
Essential Materials List:
- Pressure-treated lumber (4x4 posts, 2x4 studs, 2x6 floor joists, plywood for walls and roof)
- Concrete mix
- Roofing felt or shingles
- Exterior-grade screws and nails
- Door and window (optional)
- Weather sealant
Building the Foundation
A solid foundation is paramount for a stable shed. The simplest option is a concrete slab. Begin by excavating the area according to your shed's dimensions, ensuring a level surface. Next, construct a simple formwork (wooden frame) to contain the concrete. Pour the concrete mix into the formwork, allowing it to settle and cure for several days before proceeding. Alternatively, for a quicker solution, consider using concrete blocks or patio stones for a less permanent but still sturdy base. Remember, a level foundation prevents structural issues and makes the building process significantly easier.
Constructing the Frame and Walls
With the foundation set, begin framing the shed's walls. Assemble the wall frames using 2x4 studs, ensuring they're plumb (perfectly vertical) and square. Attach the plywood sheeting to the frames, securing it firmly with screws. Repeat this process for all four walls. Consider pre-assembling the wall frames on the ground for easier handling and alignment before lifting them onto the foundation. Accurate measurements and careful assembly at this stage are key to a structurally sound shed.
Roofing and Finishing Touches
Once the walls are up, you'll construct the roof. The simplest roof design is a gable roof (triangular shape). This requires constructing roof trusses (pre-fabricated or built on-site) and attaching them to the top plates of the walls. Cover the roof with roofing felt or shingles for weather protection. Finally, install your chosen door and window (if using), adding hinges, handles, and any necessary weather stripping. A final coat of paint or sealant protects the wood from the elements, increasing the longevity of your shed.
Building a basic shed is a manageable DIY project. By following these steps and exercising patience and precision, you can create a valuable addition to your property. Remember, safety is paramount, and don't hesitate to consult additional resources or seek help if needed. Enjoy the process and the satisfaction of creating something with your own hands!
DIY Lean-To Shed: Build a Shed Thatâs as Practical as It Is Stylish

DIY Lean-To Shed: Build a Shed Thatâs as Practical as It Is Stylish
The allure of a well-crafted outdoor structure extends beyond mere functionality. A lean-to shed, with its inherent simplicity and adaptability, presents a compelling opportunity for the discerning DIY enthusiast to create a practical and aesthetically pleasing addition to their property. This comprehensive guide will detail the process of constructing a lean-to shed, emphasizing both practical construction techniques and design considerations to ensure a structure that seamlessly integrates with its surroundings while providing ample storage or workspace.
Planning and Design: Laying the Foundation for Success
Before embarking on the construction process, meticulous planning is paramount. This involves several key steps that will significantly impact the final productâs success and longevity.
Determining Location and Dimensions:
The location of your lean-to shed is crucial. Consider factors such as proximity to existing structures, access for materials and tools during construction, and sunlight exposure. The dimensions should be carefully chosen based on your intended use. Will it serve as a simple storage shed, a workshop, or a combination of both? Accurate measurements are essential for material estimations and structural integrity.
Material Selection: Balancing Aesthetics and Durability:
The choice of materials significantly impacts both the aesthetic appeal and the longevity of your lean-to. Pressure-treated lumber is a popular choice for its resistance to rot and decay, making it ideal for the frame and foundation. For roofing, consider options such as asphalt shingles, corrugated metal, or polycarbonate panels, each offering varying degrees of durability and aesthetic appeal. Consider the local climate and anticipated weather conditions when making your selection. Furthermore, explore options for siding that complement your existing structures, maintaining a cohesive architectural style.
Permitting and Codes: Navigating Local Regulations:
Before commencing construction, itâs crucial to familiarize yourself with local building codes and permitting requirements. These regulations vary widely depending on your location and the size and complexity of your project. Obtaining the necessary permits ensures compliance and avoids potential legal issues later. Contact your local building department for specific information and guidance.
Foundation and Framing: Building a Solid Structure
The foundation and framing form the backbone of your lean-to shed. A robust and well-constructed base is crucial for ensuring stability and longevity.
Foundation Construction: Options and Considerations:
The type of foundation you choose depends on several factors, including soil conditions, budget, and the overall size and weight of the shed. Simple options include a concrete slab foundation, a gravel base, or even a raised platform using pressure-treated lumber. Each method presents different levels of complexity and cost. For a lean-to shed, a gravel base or a raised platform may suffice, provided the ground is relatively level and well-drained.
Framing the Walls and Roof: Precision and Accuracy:
Precise framing is paramount for ensuring a structurally sound and aesthetically pleasing lean-to. Start by constructing the wall frames, ensuring they are plumb and square. Use appropriate bracing to maintain stability during construction. The roof framing is equally critical. A simple lean-to roof design requires a single sloped rafter system. Carefully measure and cut the rafters to ensure proper slope and overhang. Use appropriate connectors and fasteners to secure the rafters to the wall frames. Employ appropriate techniques to ensure that the roof provides adequate water run-off and protection from the elements. Precise measurements and careful construction are critical at this stage to prevent future structural issues.
Roofing and Siding: Enhancing Aesthetics and Protection
The roofing and siding are not merely functional components; they significantly impact the overall aesthetic appeal of your lean-to shed. Careful selection and installation will greatly enhance its visual impact and longevity.
Roofing Installation: Choosing the Right Materials and Techniques:
Once the roof frame is complete, you can install the chosen roofing material. Asphalt shingles are relatively inexpensive and easy to install, offering good protection from the elements. Corrugated metal roofing is more durable and long-lasting but can be more challenging to install. Polycarbonate panels offer excellent light transmission but may be more susceptible to damage. Regardless of your choice, follow the manufacturer's instructions carefully, ensuring proper overlap and sealing to prevent leaks. Pay close attention to flashing around chimneys or other protrusions to prevent water ingress.
Siding Application: Creating a Harmonious Exterior:
The siding material should complement the overall design and surrounding environment. Consider options such as horizontal or vertical shiplap, vinyl siding, or even reclaimed wood for a rustic look. Proper installation is crucial for preventing water damage and ensuring a long-lasting finish. Ensure all seams are properly sealed and that the siding is securely fastened to the frame.
Finishing Touches and Considerations
The finishing touches are where the project truly comes to life. These details will enhance both functionality and aesthetic appeal.
Doors and Windows: Optimizing Access and Ventilation:
The type and size of doors and windows depend on the intended use of the shed. A simple shed door may suffice for storage, while a larger double door might be necessary for a workshop. Windows provide natural light and ventilation, contributing to a more pleasant workspace. Ensure that doors and windows are properly sealed and weatherproofed.
Interior Finishing: Adding Functionality and Comfort:
Interior finishing can significantly enhance the functionality and comfort of your lean-to shed. Consider adding shelving for storage, workbenches for a workshop, or even insulation for year-round use. Painting the interior walls can add a final touch of style and personality.
Safety and Maintenance: Ensuring Long-Term Durability:
Regular maintenance is crucial for preserving the longevity of your lean-to shed. Inspect the structure regularly for any signs of damage or deterioration. Address any issues promptly to prevent further problems. Consider applying a protective sealant to the wood to enhance its resistance to moisture and decay. Ensure proper ventilation to prevent mold and mildew growth. Regular cleaning will keep your shed in top condition, protecting your investment for years to come. Remember to follow all safety guidelines when working with power tools and building materials.
By meticulously following these steps, you can successfully construct a DIY lean-to shed thatâs both practical and stylish. Remember that careful planning, precise execution, and attention to detail will result in a structure that not only serves its intended purpose but also enhances the aesthetic appeal of your property for years to come.
DIY Pallet Shed: Build a Sturdy Shed for Your Garden with Pallets
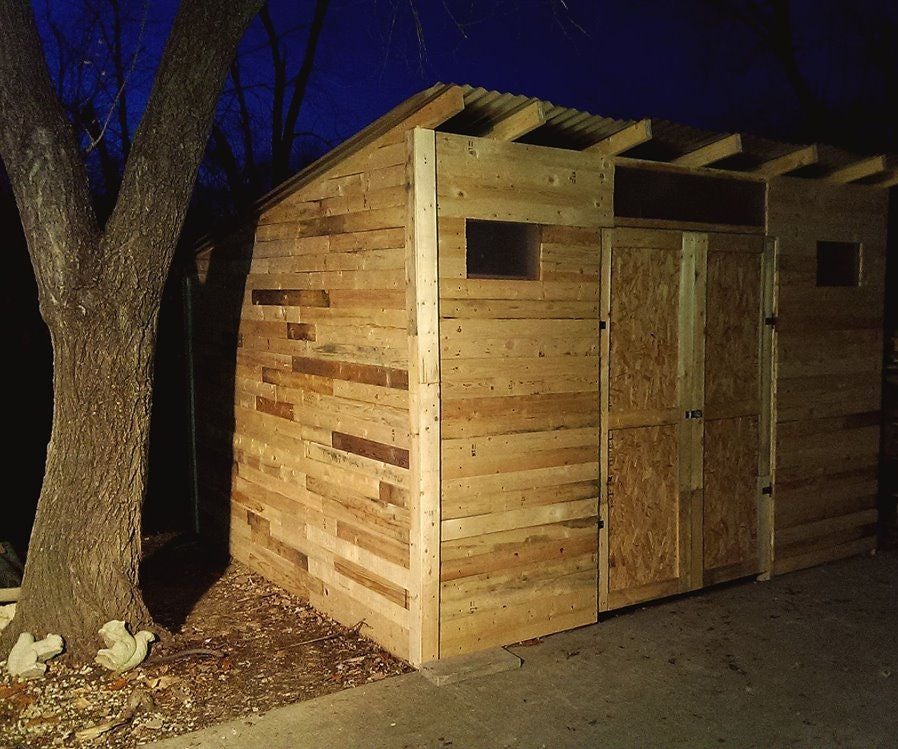
DIY Pallet Shed: Build a Sturdy Shed for Your Garden with Pallets
Hey there, fellow DIY enthusiasts! So you're thinking about building a shed, huh? And you're eyeing those free pallets sitting around? Fantastic! You're in for a treat. Building a shed from reclaimed pallets is a fantastically rewarding project that's surprisingly easier than you might think (and way cheaper than buying a pre-made one!). This guide will walk you through the process, offering tips and tricks to ensure you end up with a sturdy and functional garden shed you'll be proud of.Planning Your Pallet Shed Project
Before you even think about grabbing a hammer, some serious planning is essential. This isn't just slapping some pallets together; we're building something that'll last!Choosing Your Pallets
Not all pallets are created equal. You'll want to carefully select your pallets. Look for:- Heat-treated pallets: These are marked with "HT" and are generally safer to use for construction as they haven't been treated with harmful chemicals.
- Solid wood pallets: Avoid pallets with significant rot, warping, or broken boards. The sturdier the pallets, the sturdier your shed.
- Consistent size: Aim for pallets of a similar size to make construction easier. Measuring several pallets beforehand and choosing similar ones will save headaches down the line.
Designing Your Shed
Think about the size and features you need. How much storage space do you require? Do you need shelves? A workbench? A door? Sketch out a simple plan â" even a rough drawing on a napkin will help visualize your project. Consider the footprint of your shed and whether you'll need to obtain any permits for its placement (check local regulations). My personal recommendation? Start small. A smaller shed is easier to manage as your first pallet project. You can always build a bigger one later!Gathering Your Materials and Tools
Besides the pallets, you'll need some extra materials:- Wood screws: Lots of them! Different lengths are helpful for different applications.
- Strong wood glue:
- Metal brackets: These will add extra strength to the structure, especially at corners and joints.
- Plywood or OSB (Oriented Strand Board): For the roof and any additional sheeting you might need.
- Roofing material: Tar paper, shingles, or even heavy-duty plastic sheeting will work.
- Door hinges and handle:
- Optional: Paint or stain for weatherproofing and aesthetics.
- Hammer
- Screwdriver (or drill/driver): A drill/driver is a HUGE time-saver.
- Measuring tape
- Level
- Saw (circular saw or hand saw): For cutting pallets and additional wood.
- Safety glasses and work gloves: Always prioritize safety!
Building Your Pallet Shed: Step-by-Step
Okay, letâs get our hands dirty! Remember, this is a general guide; adjust the steps to match your specific design.Constructing the Frame
Start by assembling the base frame. This might involve laying out pallets to create the desired footprint and securing them together using wood screws and glue. Reinforce the corners using metal brackets for extra strength. You'll want your base to be perfectly level! Use a level constantly throughout this stage. No one wants a leaning shed!Adding the Walls
Once the base is solid, itâs time to build the walls. This might involve using additional pallets or constructing walls from individual pallet boards if you want a more finished look. Again, secure everything firmly with screws and glue, reinforcing with metal brackets where necessary.Building the Roof
The roof is a crucial part. You'll need to create a sturdy frame, typically using more pallets or additional lumber. Once the frame is up, you can add your plywood or OSB sheeting and then your chosen roofing material. Ensure the roof has a sufficient slope to allow for water runoff.Installing the Door
Measure, cut, and install your door. This step requires careful measuring and precise cutting. Take your time and make sure it fits perfectly! Attach hinges securely and install the handle.Finishing Touches
Once the main structure is complete, you can add any finishing touches. This might include adding shelves, a workbench, painting or staining the shed, and sealing any exposed wood to protect it from the elements.Tips for Success
- Clean your pallets: Remove any debris, nails, or loose wood before starting construction.
- Pre-drill holes: This prevents the wood from splitting when you screw it together.
- Use plenty of glue: Glue strengthens the joints and makes the structure more durable.
- Check your work regularly: Ensure everything is level and square as you go.
- Don't be afraid to ask for help: If you get stuck, ask a friend or family member for assistance.
Commonly Asked Questions
Q: How long does it take to build a pallet shed?
A: It depends on the size and complexity of your shed, but you can expect to spend anywhere from a weekend to several weekends on the project.
Q: How much does it cost to build a pallet shed?
A: The cost is primarily determined by the additional materials you need (wood screws, brackets, plywood, roofing, etc.) The pallets themselves are usually free or very inexpensive.
Q: Are pallet sheds durable?
A: With proper construction and maintenance (like sealing the wood), a pallet shed can be surprisingly durable and last for many years.
Q: What kind of permits do I need?
A: This depends entirely on your location and local building codes. Check with your local council or planning department before you start building.
Q: Can I use treated pallets?
A: While possible, it's generally recommended to avoid using chemically treated pallets due to potential health hazards. Heat-treated pallets ("HT") are a much safer option.
And there you have it! Building a pallet shed is a rewarding project that combines creativity, resourcefulness, and a good dose of elbow grease. Remember to always prioritize safety, plan carefully, and enjoy the process. Happy building!Friday, November 15, 2024
12x20 Shed with Loft: A Versatile Backyard Building

12x20 Shed with Loft: A Versatile Backyard Building
Hey there, fellow backyard enthusiasts! Thinking about adding a shed to your property? Well, let me tell you, a 12x20 shed with a loft is seriously game-changing. It's not just extra storage; it's a whole extra space that can transform your outdoor living experience. We're talking about a versatile building that can be adapted to fit your needs, whatever those may be. Let's dive into why this size and configuration is so popular, and what makes it such a smart investment.
The Perfect Size: Why 12x20?
You might be thinking, "12x20? Is that too big? Too small?" The truth is, it's just right for so many people. Itâs a great balance between ample space and manageable footprint. Think about it: a 10x12 shed might feel cramped, while anything much larger could start to feel overwhelming, especially if youâre on a smaller property.
The 12x20 dimensions provide enough floor space for a variety of uses. You can easily fit lawnmowers, gardening tools, bicycles, and other bulky items without feeling like youâre playing Tetris to find a spot. And let's not forget the real star of the show: the loft!
The Loft: A World of Possibilities
This is where things get really exciting. That loft space opens up a whole new level of versatility. Itâs not just about stacking boxes higher; itâs about creating a functional and often surprisingly spacious area. Here are some ideas to spark your imagination:
- Extra Storage: The obvious choice, and a great one! The loft is perfect for storing less frequently used items, keeping them off the main floor and maximizing your usable space.
- Workshop: If youâre a DIY enthusiast, the loft could become your personal workshop. Imagine having a dedicated space for woodworking, crafting, or repairing items, all protected from the elements.
- Home Office/Studio: With a little creativity (and perhaps some insulation!), the loft could become a quiet and inspiring workspace. Imagine working remotely with a view of your garden.
- Guest Room/Sleeping Quarters: For those unexpected overnight guests, a loft can be converted into a cozy sleeping area. Adding a comfortable mattress and some thoughtful décor can turn it into a surprisingly comfortable space.
- Storage for Seasonal Items: Keep those Christmas decorations, summer clothes, or camping gear neatly tucked away until you need them.
The possibilities truly are endless! The key is to plan carefully and think about how you want to use the space.
Building Materials and Considerations
When choosing materials for your 12x20 shed with loft, you have a few options. Consider your budget and the overall aesthetic youâre aiming for:
- Wood: A classic and aesthetically pleasing choice. Wood sheds can be painted or stained to match your home's style.
- Metal: Metal sheds are durable, low-maintenance, and often more affordable than wood. They are also resistant to pests and rot.
- Vinyl: Vinyl sheds offer a similar low-maintenance appeal to metal, with a more aesthetically pleasing finish.
Remember to consider things like:
- Foundation: A solid foundation is crucial for longevity and stability. Options include concrete, gravel, or a wooden base.
- Roofing: Asphalt shingles are a common and affordable choice, but you can also explore metal roofing for added durability.
- Insulation: If you plan on using the loft as a workspace or guest room, proper insulation is a must to maintain a comfortable temperature year-round.
- Windows and Doors: Strategically placed windows can enhance natural light and ventilation. Choose durable and secure doors.
The Cost Factor: What to Expect
The cost of a 12x20 shed with a loft can vary widely depending on the materials, features, and whether you build it yourself or hire a contractor. Expect to spend anywhere from a few thousand dollars for a basic model to tens of thousands for a fully customized, high-end structure. Doing some research and getting multiple quotes is key.
Permits and Regulations
Before you start building, itâs crucial to check with your local government for any permits or regulations that apply to shed construction. These requirements can vary depending on your location, the size of the shed, and its intended use. Ignoring these regulations could lead to fines or even be forced to dismantle your shed.
Maintenance and Care
Like any structure, your 12x20 shed with loft will require regular maintenance to keep it in top condition. Regular cleaning, occasional painting or staining (if applicable), and periodic inspections for any damage are essential.
Frequently Asked Questions
Here are some common questions people have about 12x20 sheds with lofts:
Q: How much weight can a 12x20 shed loft hold?
A: The weight capacity of a loft depends on its construction. It's always best to consult with a builder or engineer to determine the safe weight limit for your specific shed. Generally, you should avoid placing excessively heavy items in the loft.
Q: Do I need planning permission for a 12x20 shed?
A: Planning permission requirements vary by location. Check with your local council or planning authority to determine if you need permission for your specific project.
Q: Can I build a 12x20 shed with a loft myself?
A: It's possible, but it requires considerable DIY skills and experience. If you're unsure, hiring a professional builder is always a safer option.
Q: How much does it cost to build a 12x20 shed with a loft?
A: Costs vary significantly depending on materials, location, and labor. Get multiple quotes from builders to get a better understanding of the cost in your area.
Q: What kind of foundation do I need for a 12x20 shed with a loft?
A: A solid foundation is essential. Options include concrete slabs, gravel bases, or pressure-treated wooden foundations. The best option depends on your soil conditions and budget.
I hope this has given you a good overview of the benefits and considerations of a 12x20 shed with a loft. It truly is a versatile structure that can significantly enhance your property and lifestyle! Happy building!
Monday, November 11, 2024
DIY Pole Barn: How to Create a Low-Cost, High-Quality Building
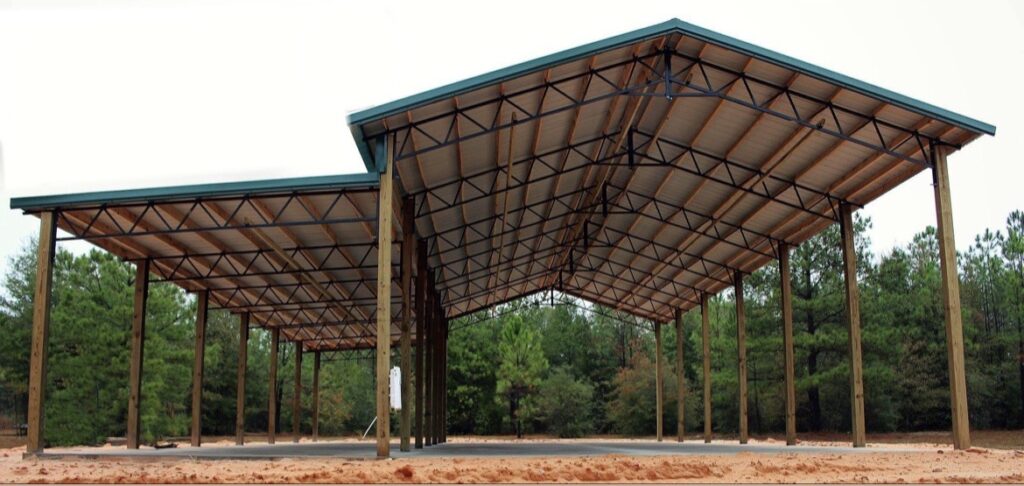
A pole barn, also known as a post-frame building, offers a versatile and cost-effective solution for a variety of purposes, including storage, workshops, garages, and even living spaces. The construction method, relying on sturdy posts embedded in concrete and a lightweight, pre-engineered frame, allows for a quick build with a minimal need for specialized labor. This guide will delve into the comprehensive process of building a DIY pole barn, equipping you with the knowledge and resources to create a durable and high-quality structure within your budget.
I. Planning & Preparation
1. Design & Planning:
Purpose: Clearly define the purpose of your pole barn. This will dictate the necessary dimensions, features, and materials.
Building Codes: Consult local building codes to ensure your project complies with regulations.
Site Analysis: Determine the ideal location on your property, considering factors like drainage, sunlight, and accessibility.
Design & Layout: Sketch your desired layout, including the dimensions of walls, doors, windows, and any other features. Consider the placement of electrical outlets, plumbing, and ventilation.
Permitting: Obtain necessary permits from local authorities before beginning construction.
2. Materials & Tools:
Foundation & Posts: Concrete footings and pressure-treated lumber for the posts.
Frame & Roof: Engineered trusses, plywood sheathing, and roofing materials.
Walls & Siding: Choose from various options like OSB, plywood, or metal siding.
Windows & Doors: Select suitable sizes and styles for your design.
Insulation & Vapor Barrier: Consider adding insulation and a vapor barrier for energy efficiency.
Hardware & Fasteners: Include screws, nails, brackets, and other essential hardware.
Tools: Basic tools like hammers, saws, screwdrivers, drills, levels, and measuring tapes are essential.
II. Construction Process:
1. Foundation:
Excavation: Dig holes for the concrete footings, ensuring they are deep enough to reach frost-free soil.
Forms: Build forms around the holes to create the desired footing dimensions.
Rebar: Install rebar within the forms for reinforcement.
Concrete Pouring: Carefully pour concrete into the forms, ensuring it is properly compacted.
Curing: Allow the concrete to cure properly before proceeding to the next step.
2. Post Installation:
Post Preparation: Cut and treat the post lumber with a sealant to prevent rot.
Setting Posts: Position the posts in the concrete footings and ensure they are plumb and level.
Temporary Bracing: Brace the posts with temporary supports until the concrete fully cures.
3. Framing:
Truss Installation: Raise and secure the pre-engineered trusses to the posts, creating the roof frame.
Wall Sheathing: Attach plywood or OSB sheathing to the posts, creating a solid wall structure.
Window & Door Openings: Cut openings in the sheathing for windows and doors.
4. Roofing:
Roof Sheathing: Install plywood or OSB sheathing on top of the trusses.
Underlayment: Lay down felt underlayment for water resistance.
Roofing Shingles: Install your chosen roofing material, following manufacturer instructions.
Venting: Install roof vents to ensure proper ventilation and prevent moisture buildup.
5. Siding & Finishing:
Siding Installation: Apply your chosen siding material, adhering to manufacturer guidelines.
Windows & Doors: Install windows and doors, ensuring proper sealing and weatherproofing.
Interior Finishing: Finish the interior walls with drywall, paint, or other desired materials.
Electrical & Plumbing: Install electrical wiring and plumbing fixtures as needed.
III. Cost-Saving Strategies:
DIY Labor: By doing most of the work yourself, you can significantly reduce labor costs.
Material Sourcing: Shop around for the best prices on materials, considering bulk purchases and sales.
Basic Design: Opt for a simple design with fewer features to minimize material requirements.
Recycled Materials: Consider using recycled materials for certain components like siding or roofing.
Alternative Insulation: Explore affordable insulation options like fiberglass batts or blown-in cellulose.
IV. Quality Considerations:
Foundation & Posts: Choose high-quality concrete and pressure-treated lumber for a long-lasting structure.
Trusses: Ensure your trusses are designed and engineered by a qualified professional.
Roofing & Siding: Invest in durable and weather-resistant roofing and siding materials.
Proper Ventilation: Implement proper ventilation throughout the structure to prevent moisture buildup.
Maintenance: Regular maintenance is crucial for preserving the longevity and quality of your pole barn.
V. Additional Considerations:
Accessibility: Plan for accessibility features if your pole barn will be used for storage or as a workshop.
Climate: Consider your local climate when selecting materials and designing your pole barn for optimal performance.
Future Expansion: Plan for the possibility of future expansion by leaving room for additional posts or bays.
VI. Conclusion:
Building a DIY pole barn can be a rewarding experience, allowing you to customize your space to your specific needs and budget. By carefully planning, sourcing materials wisely, and adhering to proper construction techniques, you can create a durable, high-quality structure that will serve you for years to come.
Remember, safety should always be a top priority. Wear proper safety gear and follow manufacturer guidelines for all tools and materials. Seek professional guidance when necessary, and don't hesitate to ask for help from experienced individuals. With dedication and proper planning, you can successfully build a DIY pole barn that meets your unique requirements and becomes a valuable asset to your property.
How to Design a Pole Barn with a Natural Wood Aesthetic

Pole barns, with their straightforward construction and adaptable design, have long been a favorite choice for homeowners seeking functional and durable structures. But beyond practicality, pole barns offer a unique opportunity to embrace the beauty of natural materials, crafting spaces that resonate with warmth and rustic charm. Designing a pole barn with a natural wood aesthetic requires a meticulous approach, blending structural integrity with the elegance of unadulterated wood.
Foundation and Framing: The Essence of Strength and Simplicity
The foundation of a natural wood pole barn lies in its sturdy, exposed posts. Choosing the right timber is paramount. Reclaimed timbers, with their rich patina and history, impart a timeless elegance. Alternatively, new timbers like Douglas fir, cedar, or pine offer durability and a natural beauty that can be enhanced with oil finishes. The posts should be carefully chosen for their straightness and uniformity, creating a foundation of architectural grace.
The roof trusses, ideally constructed from exposed timber beams, become an integral part of the aesthetic. Consider using heavy timber trusses, showcasing the grain and knots of the wood. They offer a sense of rustic grandeur, adding a captivating element to the overall design.
Walls: Embracing the Natural Texture
The walls of a pole barn present a canvas for showcasing the beauty of wood. Several options exist:
Traditional Siding: Vertical or horizontal wood siding, whether rough-sawn or smooth-planed, provides a classic rustic look. Choose a natural wood stain or paint to accentuate the grain and texture.
Shiplap Siding: Shiplap offers a timeless and visually appealing aesthetic, with its overlapping boards creating a textured and inviting surface.
Board and Batten: This traditional siding method utilizes vertical boards with narrow battens covering the gaps, creating a distinctive and elegant look.
Roof: A Capstone of Natural Elegance
The roof, a defining feature of any pole barn, provides an opportunity to accentuate the natural wood theme. A standing seam metal roof, in a dark color that complements the wood, offers durability and a sleek modern aesthetic. Alternatively, a traditional wood shingle roof, with its inherent rustic charm, offers a more traditional look.
Windows and Doors: Framing Views and Welcoming Entrances
Windows and doors are critical design elements, framing views and welcoming guests. Large windows, ideally with a rustic charm, allow ample natural light to flood the interior. Consider using salvaged windows with panes of frosted or patterned glass for a unique and vintage touch.
Doors, crafted from solid wood with simple hardware, should complement the overall rustic theme. A double Dutch door, with its charming design and practicality, adds a touch of elegance.
Interior Design: Embracing Rustic Charm
The interior of a natural wood pole barn should be a reflection of the rustic aesthetic established on the exterior.
Flooring: Hardwood flooring, especially reclaimed barn wood or wide-plank oak, provides a warm and inviting surface. Concrete floors, stained with natural tones, can add a modern industrial touch.
Walls: Exposed beams and wood walls, finished with a natural wood stain or clear coat, create a welcoming and inviting atmosphere.
Lighting: Natural light should be maximized, but strategically placed pendant lights or wall sconces, crafted from reclaimed wood or metal, can add a touch of rustic charm.
Furniture: Choose rustic furniture made from reclaimed wood, handcrafted leather, or metal with a weathered patina.
Sustainability: A Commitment to Nature
A key principle in designing a natural wood pole barn is incorporating sustainable practices. Choose locally sourced lumber, minimizing the environmental impact of transportation. Explore using reclaimed wood, giving old timbers a second life and reducing waste.
The Art of Finishing Touches: Enhancing the Natural Beauty
The finishing touches are crucial in creating a cohesive and elegant design.
Natural Wood Stains: Use stains that enhance the natural beauty of the wood, highlighting the grain and knots.
Weathering and Patina: Allowing wood to age naturally, developing a soft patina, adds character and depth to the design.
Hardware: Choose simple, rustic hardware that complements the natural wood aesthetic.
Conclusion: A Haven of Natural Beauty
Designing a pole barn with a natural wood aesthetic is more than simply choosing materials. It's about embracing the inherent beauty of nature and crafting a space that is both functional and visually captivating. By carefully selecting materials, embracing sustainable practices, and adding thoughtful design touches, a pole barn can become a haven of rustic charm, a testament to the enduring beauty of nature and the art of traditional craftsmanship.
DIY Guide to Building a Pole Barn for Farm Use and Livestock Care
A pole barn, also known as a post-frame building, offers a versatile and cost-effective solution for various farm needs, from livestock housing and equipment storage to workshops and hay storage. Building your own pole barn can be a rewarding experience, allowing you to tailor the structure to your specific requirements and save on construction costs. This comprehensive guide outlines the steps involved in designing, planning, and constructing a pole barn suitable for farm use and livestock care.
1. Planning and Design:
a) Determining Your Needs:
Purpose: Define the primary purpose of your pole barn. Is it for housing livestock, storing equipment, or a combination of both?
Size: Estimate the necessary square footage based on your intended use. Consider the number of animals, equipment storage needs, and future expansion potential.
Location: Choose a suitable location on your property, considering access, drainage, and proximity to utilities.
Building Codes: Consult with your local building department to understand zoning regulations, setback requirements, and any specific building codes.
b) Design Considerations:
Foundation: Post-frame buildings are typically supported by concrete piers embedded in the ground. Consider the soil conditions and frost line to ensure adequate foundation stability.
Framing: Pole barns rely on large-diameter, pressure-treated poles (typically 6x6 or 8x8) to support the roof and walls. The spacing and size of the poles will depend on the buildingâs size and snow load.
Roofing: Choose a roofing system that meets your budget and climate. Metal roofing is popular due to its durability, longevity, and low maintenance requirements.
Siding: Consider siding options that are weather-resistant and aesthetically pleasing, such as metal siding, vinyl siding, or wood siding.
Doors and Windows: Select doors and windows that provide adequate ventilation and access while minimizing energy loss.
Ventilation: Proper ventilation is crucial for livestock housing. Consider installing ridge vents, gable vents, or fan systems to ensure adequate airflow.
Insulation: If temperature control is a concern, consider adding insulation to the walls and roof.
2. Obtaining Permits and Materials:
Building Permit: Submit your plans to the local building department for approval.
Materials: Obtain a detailed materials list from your chosen supplier. This should include:
Poles: Pressure-treated timber, typically 6x6 or 8x8, depending on size and snow load.
Concrete: For piers and footing.
Roofing: Metal panels, sheathing, and underlayment.
Siding: Metal, vinyl, or wood siding panels.
Doors and Windows: Choose materials and sizes based on your needs.
Fasteners: Structural screws, nails, bolts, and clips.
Other Materials: Hardware, insulation, flashing, trim, etc.
3. Site Preparation:
Clear the Site: Remove any trees, vegetation, or debris from the designated building area.
Leveling: Use a laser level or a surveyor's transit to accurately level the site.
Excavation: Dig holes for the concrete piers, ensuring adequate depth based on frost line and local building codes.
4. Foundation Construction:
Concrete Piers: Pour concrete into the excavated holes, ensuring proper reinforcement and compaction. Allow the concrete to cure according to manufacturer recommendations.
Anchor Bolts: Install anchor bolts in the concrete piers to secure the poles.
5. Pole Installation:
Erecting the Poles: Carefully lift the poles into place, ensuring they are plumb and aligned with the anchor bolts.
Securing the Poles: Bolt the poles to the anchor bolts and temporarily brace them until the roof is installed.
6. Roof Framing and Sheathing:
Roof Trusses: Install prefabricated roof trusses or construct custom trusses on site.
Sheathing: Attach plywood or OSB sheathing to the roof trusses to create a solid surface for the roofing.
7. Roofing Installation:
Underlayment: Install a waterproof underlayment over the sheathing.
Roofing Panels: Secure the metal roofing panels to the sheathing, overlapping them according to manufacturer instructions.
8. Wall Framing and Siding:
Wall Studs: Install wall studs between the poles, using pressure-treated lumber for the bottom plate.
Siding: Attach the chosen siding material to the wall studs.
9. Doors and Windows:
Installation: Install the doors and windows according to manufacturer instructions, ensuring proper weather sealing.
10. Interior Finishes:
Floor: Install a suitable flooring material, such as concrete, wood, or composite decking.
Interior Walls: Consider adding insulation, drywall, or other finishes to improve aesthetics and thermal performance.
Electrical Wiring: Hire a qualified electrician to install electrical wiring and fixtures.
11. Final Touches:
Painting or Staining: Apply paint or stain to the exterior and interior surfaces, as desired.
Gutter and Downspouts: Install gutters and downspouts to direct rainwater away from the foundation.
Landscaping: Landscaping around the pole barn can enhance aesthetics and protect the foundation from erosion.
12. Livestock Care Considerations:
Ventilation: Ensure adequate ventilation to prevent moisture build-up and maintain a healthy environment for livestock.
Lighting: Install sufficient lighting for visibility and animal well-being.
Water and Feed Systems: Install appropriate water and feed systems based on the type and number of animals.
Manure Management: Plan for a system to remove and dispose of animal waste.
Safety: Consider safety measures for both humans and livestock, such as fencing, gates, and secure storage of hazardous materials.
13. Resources and Support:
Building Codes: Consult with your local building department for specific codes and regulations.
Professional Contractors: Consider hiring a qualified contractor for specific tasks, such as foundation work, electrical wiring, or roofing installation.
Pole Barn Manufacturers: Many companies specialize in pole barn construction and can provide design assistance, materials, and installation services.
Farm Supply Stores: Purchase materials and supplies from reputable farm supply stores.
Conclusion:
Building a pole barn for farm use and livestock care requires careful planning, design, and execution. By following this comprehensive guide, you can ensure a successful construction project that provides a durable and functional structure for your farm needs. Remember to consult with professionals, follow local building codes, and prioritize safety throughout the construction process. With proper attention to detail, you can create a pole barn that will serve your farm for years to come.
How to Build a Pole Barn with a Durable Metal Roof

Alright, you want to build a pole barn with a metal roof, huh? You've come to the right place! Building a pole barn is a great way to get some extra storage space, a workshop, or even a garage. And if you want a roof that's gonna last, metal is the way to go! It's strong, durable, and can stand up to all kinds of weather.
First things first, let's talk about planning. Building a pole barn is a pretty big project, so you'll need to get your ducks in a row before you start.
Figure out the size and shape: What are you gonna use this barn for? How much stuff do you need to store? Do you need a big, open space or something more compartmentalized? Once you know what you need, you can start drawing up some plans.
Choose a location: Make sure it's a level spot with good drainage. Also, consider the wind direction and any potential snow loads.
Get the necessary permits: Depending on where you live, you might need a building permit. Don't be a rebel â" check with your local authorities before you start digging. It's better to be safe than sorry, trust me.
Gather your materials: You'll need concrete, lumber, metal roofing panels, fasteners, and all the usual tools for building a structure.
Now let's dive into the actual construction:
1. Prepare the site: Start by clearing the area and marking out the footprint of your barn. You'll need to dig post holes for your poles, and you'll need to make sure those holes are deep enough to support the weight of the barn.
2. Set the poles: You'll be using treated lumber for the poles, and they'll be set into the concrete. Make sure the poles are plumb and level, and that they're spaced according to your plans. Once the poles are set, you can pour concrete to secure them.
3. Build the frame: This part is where you start to see your barn take shape! You'll be using lumber to connect the poles and create the walls and roof. Make sure your framing is strong and secure.
4. Sheathing and roofing: Now it's time for the metal roofing! First, you'll need to install sheathing, which acts as a base for the roofing panels. Make sure you use the right type of sheathing for metal roofing â" plywood or OSB is usually a good choice.
5. Install the metal roof: Now for the fun part! There are different types of metal roofing, like standing seam, corrugated, and metal shingles. You'll need to choose the type that's best for your climate and budget. And remember, you'll need to install a felt underlayment before you put down the metal panels. This will help with waterproofing and soundproofing.
Here's a breakdown of different metal roofing types:
Standing Seam: This is a popular choice for pole barns. It's strong, durable, and has a sleek, modern look. The panels are installed vertically with interlocking seams that create a tight seal.
Corrugated: This is another classic choice for pole barns. It's very durable and cost-effective. It's also easy to install. But it's not as sleek as standing seam.
Metal Shingles: These are designed to mimic the look of traditional shingles, but they're made of metal. They're a good option if you want a more traditional look but still want the benefits of metal roofing.
Once you've installed the metal roof, you'll need to add a few finishing touches:
Fascia: This is the trim board that goes around the edge of the roof. It's important for giving your barn a finished look and protecting the roof from the elements.
Gutters and downspouts: These will help to direct rainwater away from the foundation of your barn.
Here are some extra tips for installing a metal roof:
Use the right fasteners: Don't just grab any old screws! Make sure you use fasteners that are designed for metal roofing. They'll need to be corrosion-resistant and long enough to penetrate the sheathing and framing.
Overlap the panels properly: You need to overlap the panels enough to ensure a watertight seal. The amount of overlap will depend on the type of metal roofing you're using.
Be careful around the edges: You'll need to pay extra attention to the edges of the roof, especially around the eaves and rakes. Use flashing to create a waterproof seal.
Alright, so you've got your metal roof on, and your pole barn is looking pretty great! Now, here are a few things to keep in mind:
Maintenance: Even though metal roofing is durable, it still needs some basic maintenance. Inspect it regularly for any signs of damage or corrosion. You'll also want to keep the roof clean, removing any debris that might build up.
Insulation: Metal roofs can get hot in the summer and cold in the winter. If you're planning on using the barn year-round, you'll need to think about insulating it. You can add insulation to the walls and roof to help keep the temperature inside more comfortable.
Ventilation: If you're going to have a workshop or garage in your barn, you'll need to think about ventilation. This will help to prevent moisture build-up and keep the air fresh.
And remember, this is just a basic guide. Building a pole barn is a pretty involved process, and it's always a good idea to consult with a professional if you're not sure about anything. But with some planning and careful attention to detail, you can build a sturdy and durable pole barn with a long-lasting metal roof. You'll be able to store all your stuff, work on your projects, or just enjoy the space for years to come!
Sunday, November 10, 2024
Step-by-step guide to building an affordable 8x10 shed
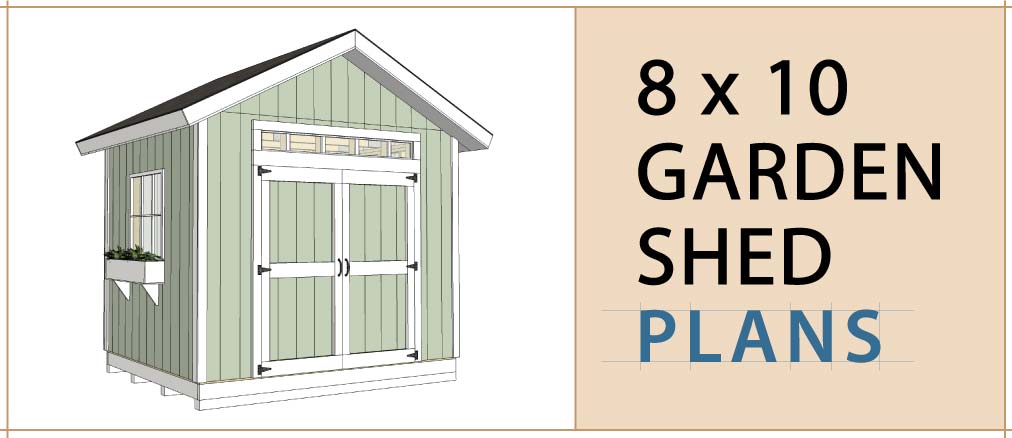
Hey there, fellow DIY enthusiast! Want a shed, but don't want to break the bank? You're in the right place! Building an 8x10 shed is a great way to get extra storage space without emptying your wallet. We're going to walk through the process, step by step, keeping it as simple and affordable as possible.
Let's Get Started!
First things first, let's talk about what you'll need. Here's a list of materials, tools, and supplies:
Materials:
Lumber: You'll need pressure-treated lumber for the foundation and floor joists, and standard framing lumber for the walls and roof.
Sheathing: Plywood or OSB for the walls and roof.
Roofing: Choose from asphalt shingles, metal roofing, or even a cool membrane roof.
Windows and Doors: Decide on the size and number of windows and doors you need.
Siding: Choose a siding material that suits your budget and style.
Paint or Stain: For a finished look, paint or stain the exterior and interior of your shed.
Hardware: Nails, screws, brackets, hinges, etc.
Tools:
Circular saw: For cutting lumber.
Tape measure: For accurate measurements.
Level: To ensure your shed is perfectly level.
Hammer: For hammering nails.
Drill/Driver: For driving screws and drilling holes.
Safety Glasses: To protect your eyes.
Work Gloves: For safe handling of materials.
Step 1: Planning and Design
Before you even step foot in a lumber yard, take some time to plan your shed.
Location: Choose a spot with good drainage and access for your tools and materials.
Foundation: Decide on the type of foundation: concrete slab, gravel pads, or even just a simple wooden frame.
Style: Think about the overall style of your shed. Do you want a traditional, modern, or rustic look?
Door and Window Placement: Plan where you want your doors and windows for easy access and light.
Step 2: Building the Foundation
Now it's time to lay the groundwork for your shed. This is where your foundation type comes into play. Here's how to build a simple wooden frame foundation:
1. Mark the area: Use stakes and string to mark out the dimensions of your shed.
2. Set the foundation posts: Dig holes for your foundation posts and set them in concrete. Make sure the posts are level and spaced according to your design.
3. Connect the posts: Use pressure-treated lumber to connect the posts and create the frame for your shed.
Step 3: Building the Floor
The floor is the base of your shed, so it's important to get it right.
1. Lay the joists: Install the floor joists over the foundation posts, making sure they're spaced 16 inches apart. Attach them securely to the posts.
2. Add subfloor: Lay plywood or OSB sheathing over the joists to create the floor. Make sure the sheets are staggered for added strength.
Step 4: Building the Walls
Time to get those walls standing tall!
1. Construct the wall frames: Cut and assemble the wall frames using your framing lumber.
2. Install the sheathing: Attach plywood or OSB sheathing to the wall frames.
3. Erect the walls: Carefully lift and secure the wall frames onto the floor, making sure they're plumb and level.
Step 5: Building the Roof
The roof is the final layer of your shed. It's time to get creative!
1. Create the roof trusses: Build your roof trusses according to your chosen roof design. There are plenty of online resources that can guide you.
2. Install the trusses: Place the trusses onto the walls, making sure they are level and securely attached.
3. Add roof sheathing: Cover the roof with plywood or OSB sheathing.
Step 6: Finishing Touches
It's time to add those finishing touches that will turn your shed from a skeleton to a beautiful, functional space.
1. Install siding: Choose your siding material and install it over the sheathing.
2. Install doors and windows: Mount the doors and windows in their designated spots.
3. Add roofing: Securely install your chosen roofing material.
4. Paint or stain: Give your shed a fresh coat of paint or stain to protect it and enhance its appearance.
Tips for Saving Money:
Buy lumber in bulk: This can save you money, especially on larger projects.
Look for deals: Check online marketplaces and local lumber yards for discounted materials.
Reclaim materials: If you're feeling crafty, use reclaimed wood or other materials to add a unique touch and save on costs.
Do the work yourself: Hiring contractors can be expensive, so try to do as much of the work yourself as possible.
Conclusion:
Building your own 8x10 shed can be a rewarding experience! Not only will you save money, but you'll also gain valuable skills and have a sense of accomplishment. Remember, take your time, plan carefully, and don't be afraid to ask for help if needed.
With this guide and a little elbow grease, you'll be enjoying your very own affordable shed in no time! Happy building!
Building an 8x12 shed? hereâs how to do it cheaply

Alright, so you're thinking about building a shed. Maybe you need a place to store your tools, garden equipment, or maybe just a quiet space to escape the chaos of life. But the thought of hiring a contractor makes your wallet cringe. Don't worry, building your own shed can be a rewarding and cost-effective project! I'm here to guide you through it, step-by-step, and show you how to build an 8x12 shed on a budget.
First Things First: The Plan
The first step is to get your head in the game. Before you even start buying lumber, you need a plan. This doesn't mean you have to be an architect, but it does mean having a clear vision of what you want. Here are some key things to consider:
Shed Style: Do you want a simple, single-slope roof or a more traditional gable roof? Maybe you're feeling fancy and want a Dutch gambrel? The roof style will influence the amount of lumber you'll need and the overall complexity of the build.
Doors and Windows: Think about how you'll access your shed and how much light you want inside. A standard single door is usually sufficient, but you might need a double door for larger items. Consider adding a window or two for natural light and ventilation.
Foundation: This is a critical decision. You have several options, from simple concrete blocks to a poured concrete foundation. The choice depends on your budget, the soil conditions, and the weight of the shed. For a basic 8x12 shed, a concrete block foundation is usually sufficient and cost-effective.
Materials: Do you want to go with traditional wood framing, or explore cost-effective options like metal siding or pre-engineered shed kits? Each material has its pros and cons, and you need to weigh them against your budget and your DIY skills.
The Foundation: The Groundwork for Your Shed
Once you have a general plan, you can start focusing on the foundation. This is the most important part of the build because it needs to be strong and level to support the weight of the shed.
Leveling the Ground: The first step is to level the ground where you'll be building. This means clearing away any debris, removing any bumps or dips, and ensuring that the ground is perfectly flat. You can use a level and a shovel to do this. Remember, a little effort now will make the rest of the build much easier.
Concrete Block Foundation: For a simple shed, a concrete block foundation is the most common and affordable option. You'll need to purchase enough blocks to create a perimeter wall around the footprint of the shed. The blocks should be laid in a bed of mortar, with the top of the block foundation level with the surrounding ground.
Anchoring the Foundation: Once the block foundation is laid, you need to anchor it to the ground. This prevents the foundation from shifting or settling over time. You can do this by drilling holes into the concrete blocks and inserting anchor bolts.
Framing: The Skeleton of Your Shed
With the foundation in place, it's time to start framing the walls and roof of your shed. This is where things start to get exciting.
Framing the Walls: You'll need to cut and assemble wall studs, plates, and headers. This involves using a circular saw, a level, and a hammer. If you're going with a traditional wood frame, you'll need to decide on the stud spacing, which is typically 16 inches on center.
Building the Roof: The roof is the next step. You'll need to cut and assemble rafters, joists, and sheathing. This can be a bit more challenging than framing the walls, so if you're not confident in your DIY skills, it might be helpful to enlist the help of a friend or family member. Be sure to choose the right roof pitch for your location and the type of roofing you plan to use.
Adding Doors and Windows: Once the walls and roof are framed, it's time to add your doors and windows. This involves cutting openings in the walls, installing the door and window frames, and attaching the doors and windows.
Sheathing and Siding: The Skin of Your Shed
Now it's time to cover up the framing with sheathing and siding. This will protect the structure from the elements and give your shed a finished look.
Sheathing: The sheathing goes directly onto the framing. This is typically plywood or OSB (oriented strand board), which provides a solid base for the siding.
Siding: The siding is the final layer that gives your shed its exterior look. You have a wide range of options here, from traditional wood siding to metal siding, vinyl siding, or even reclaimed materials like pallets or corrugated metal.
Roofing: Keeping the Rain Out
With the walls sheathed and sided, it's time to tackle the roof.
Underlayment: Before installing the roofing material, you need to lay down a layer of underlayment. This is a waterproof membrane that protects the sheathing from moisture and prevents leaks.
Roofing Material: You have tons of options for roofing materials, from asphalt shingles to metal roofing, or even cedar shakes. Choose the material that best fits your budget and style.
Finishing Touches:
Now for the fun part! Adding the finishing touches will make your shed truly your own.
Painting or Staining: A fresh coat of paint or stain will give your shed a polished look. Choose colors and finishes that complement your house or your outdoor space.
Flooring: A simple concrete floor might suffice for a basic shed, but you can also add a wood floor for comfort and style. This can be done with plywood or even tile for a more finished look.
Interior Trim and Finishing: Add some finishing touches inside, like molding around the doors and windows. Consider adding shelves, hooks, or even a workbench for extra storage and functionality.
Final Thoughts
Building a shed is a rewarding project that you can do yourself, and it doesn't have to break the bank. With a little planning, patience, and a lot of elbow grease, you can create a custom shed that perfectly fits your needs and enhances your outdoor space. Remember to take your time, enjoy the process, and don't be afraid to ask for help from friends, family, or experienced DIYers.
Now go out there, grab your tools, and build something amazing!